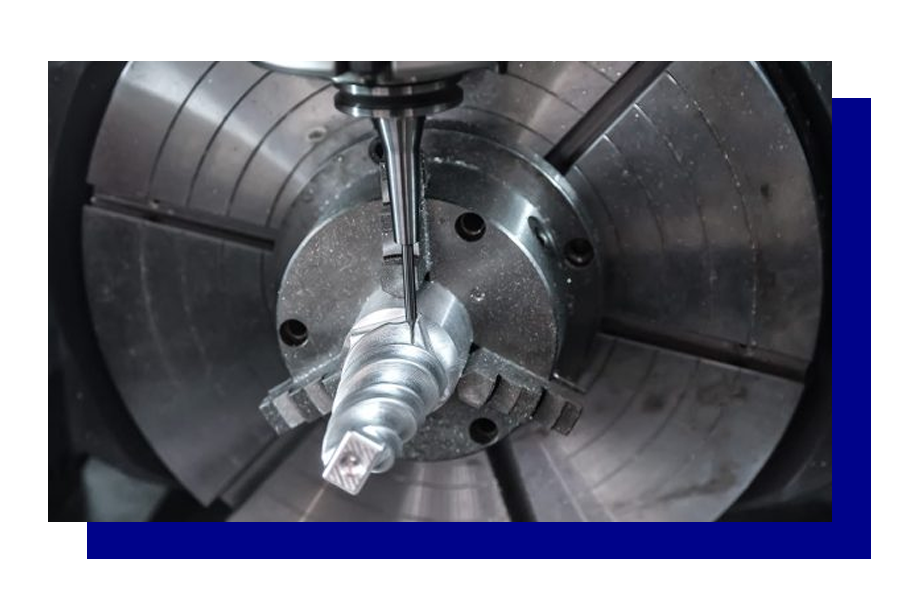
Для удовлетворения потребностей развития гибкости и автоматизации производства степень яркости станков с ЧПУ постоянно повышается. Как и любая другая системообразующая отрасль, услуги металлообработки постоянно совершенствуются и развиваются, чтобы предлагать качественные изделия. Это находит явное отражение в следующих аспектах:
- Технология адаптивного управления процессом: путем мониторинга силы резания в процессе обработки, мощности шпинделя и двигателя подачи, тока, напряжения и другой информации, использования традиционных или современных алгоритмов идентификации, определения силы инструмента, износа, состояния поломки и стабильности состояния обработки станка, и в соответствии с этими состояниями в реальном времени регулируются параметры металлообработки (скорость шпинделя, скорость подачи) и инструкции по обработке, так что оборудование в целях повышения точности обработки, снижения шероховатости поверхности и повышения безопасности эксплуатации оборудования.
- Интеллектуальная технология самодиагностики и самовосстановления неисправностей: на основе имеющейся информации о неисправностях применяются современные интеллектуальные методы, позволяющие быстро и точно определить местонахождение неисправности.
- Интеллектуальная технология воспроизведения и моделирования неисправностей: возможность записи всей системы различной информации, возникновение множества ошибок и аварий на станках с ЧПУ для воспроизведения и моделирования, определения причин ошибок, поиска решений проблем, накопления производственного опыта для более качественного оказанная услуг металлообработки.
- Интеллектуальный сервопривод переменного тока: может автоматически определять нагрузку и настраивать параметры интеллектуальной сервосистемы, включая интеллектуальный сервопривод шпинделя и интеллектуальное сервоустройство подачи. Такое приводное устройство может автоматически определять вращательную инерцию двигателя и нагрузки и автоматически оптимизировать и настраивать параметры системы управления таким образом, чтобы система привода могла получить наилучший режим работы.
- Интеллектуальная система ЧПУ 4M: в процессе производства, обработки, тестирования интеграция направлена на достижение быстрого производства, быстрого обнаружения и быстрого реагирования на практические действия. Измерение, моделирование, обработка, управление станком интегрируются в систему 4M для обмена информацией и содействия интеграции измерения, моделирования, обработки, зажима и управления.
Тенденцией и направлением развития станков с ЧПУ, т.е. быстрых, точных, сложных, интеллектуальных, открытых, параллельных, сетевых и экстремальных станков, стало их развитие. Как будут развиваться эти тенденции в новом году? В каком направлении будет развиваться обработка? Будут ли новые технологические инновации улучшать услуги ЧПУ? Каковы тенденции роста? Об этом мы пишем ниже!
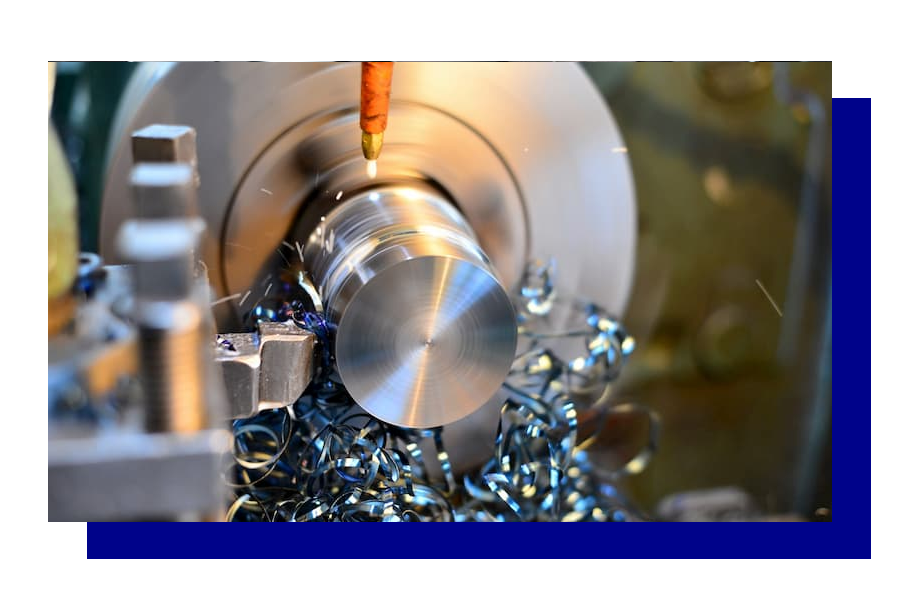
Повышение скорости обработки на станках с ЧПУ как основа для предоставления услуги металлообработки
В связи с бурным развитием таких отраслей, как автомобилестроение, национальная оборона, авиационная и космическая промышленность, а также с использованием новых материалов, например алюминиевых сплавов, требования к обработке на станках с ЧПУ становятся все выше. Станки с ЧПУ обеспечивают в этих случаях:
- Скорость вращения шпинделя: в станке используется электрический шпиндель (встроенный шпиндельный двигатель), максимальная скорость вращения шпинделя составляет 200000 об/мин.
- Скорость подачи: разрешающая способность составляет 0,01 мкм, а максимальная скорость подачи станка при обработке сложных и точно обработанных поверхностей достигает 240 м/мин.
- Скорость вычислений: динамичное развитие микропроцессоров гарантирует быстрый и точный прогресс систем числового программного управления. В результате процессоры эволюционируют в 32- и 64-разрядные системы числового программного управления, а частота увеличивается до сотен мегагерц и гигагерц. Благодаря вычислениям значительно повысилось быстродействие, и скорость подачи до 24-240 м/мин по-прежнему может достигаться с разрешением 0,1 мкм и 0,01 мкм
- Скорость смены режущего инструмента: в настоящее время смены используемого режущего инструмента в передовых зарубежных станках обычно составляет около 1 с, а максимальное время может достигать 0,5 с.
При подготовке материала бывли использована информация, предоставленная специалистами компании Артель https://tltartel.ru/